Carving, Karma, and Culture Resources
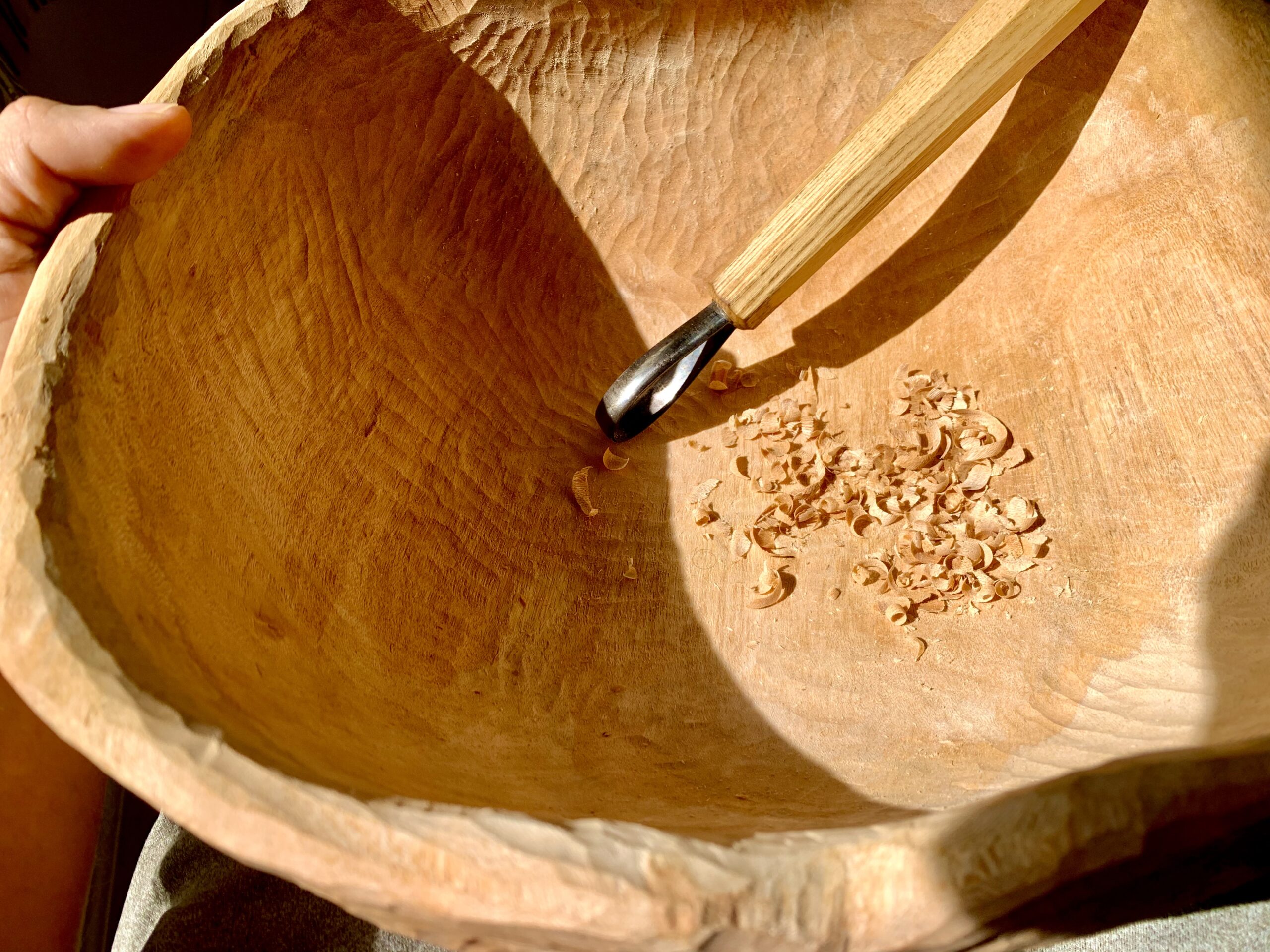
From heart to hand to knife to wood
May this kamma promote the good
The heart, the hand, the knife, the wood
May each be loved and understood
Zoom Recordings
will be posted here
Link to recording of 1st Class – Monday, September 9th
Link to recording of 2nd Class – Monday, September 16th
Link to recording of 3rd Class – Monday, September 23rd
Link to recording of 4th Class – Monday September 30th
Link to recording of 5th Class – Monday, October 7th
Next meeting, Monday November 4th!
Technical Stuff
Some knife grip explanations from a famous Swedish Carver. (He actually has a bunch!)
I realized that most folks have long bowl blanks that will create an oblong bowl. You likely won’t be able to do this whole maneuver on your wood, but you can see how an oval shape can be made by connecting two circles – even if you don’t do it quite this exactly…
Finishing Work
If you decided to go down the rabbit whole of philosophies of sanding, burnishing, oiling, I am sure you will find some basic principles and plenty of conflicting advice. Just like with knife sharpening. I learned to sand my woodwork, but now I mostly just burnish it. There are different advantages to both, and of course plenty of folks who actually do both do the same pieces of work.
For sanding, essentially, you want to begin with a more coarse sand paper and progressively more to more fine sandpaper. How many imperfections do you want to wash away? How much evidence of human labor do you want to wash away? A more coarse sanding will remove more, and then when you get to a more fine paper, you will have a very smooth surface. But you can also just use a fine grade paper, and more of your knifework will be visible at the end. You can start with 80grit, go onto 100, then 220, then 400, then 600 as a more polish. You can just do 220 and 400. You can just do 200. Depends on what you want as a final product, and how boring (and dusty) you feel sanding is.
If you sand a spoon or bowl and then use it with liquid, you will notice that the grain pops out again after washing. You can re-sand it again after that, and after a few times of this process, the grain will stop popping out and the wood will stay more polished even after washing. You can do this on purpose as part of your process: Sand, then rinse your work in water and dry it with a towel. Once it is fully dry again, go sand again. Rinse again. Dry Again. Sand again. After 3 times, this usually does the trick. Then you can oil.
Again, usually nut oils or some seed oils (walnut, almond, kukui, jojoba, tung, argon, linseed) are more stable over the long term than most cooking oils (olive, canola, coconut). Mineral oil is considered “food safe” and is used on cutting boards and stuff a lot – though it is petroleum based. Some folks melt beeswax into their oils. I have not done that, and it doesn’t seem super necessary – but could be interesting protection for a bowl. Usually, you will need to apply oil over a period of a few days. Apply, rub it in – the warmth of your massaging will help the wood absorb the oil. Let it soak in. Apply more in a few hours or the ext day. Do this until it has the sense of being saturated. This will prevent water from coming in and going out of the wood grains – a process that is destructive to wood over time. You can wash your bowls, but be sure to dry them right away with a towel and know that warm soapy water will remove some of the protective oils – so you will need to reapply oil after washing sometimes. Over the years this becomes less necessary, and you maybe only need to oil something once a year, if you are washing it a lot. Some people oil and then put in an oven – or the sun – for the heat. Just know there are many approaches.
An alternative to sanding, is simply burnishing with a hard, rounded, object. You can sand and burnish, apparently. Burnishing is really doing something different: it is compressing the fibers in a more direct way, and can help stabilize and give a gloss to the work, as you can see in the video below. It also maintains more of a sense of the cuts and work. Can be done dry and/or wet (oiled).
Here is a pretty good start-to-finish spoon making video. You can see a bit of axe work and then see how he uses his knife to cut a signature in it – for those who want to mark their work!
Tool Care
I will add some videos on sharpening soon…
For Consideration
Jesse’s recent essay on work, spoon-carving, karma, Marx, and apple pie.
Mangala Sutta link
Bāhusaccañca sippañca vinayo ca susikkhito Subhāsitā ca yā vācā etaṃ maṅgalamuttamaṃ
To be knowledgeable, skilled in crafts, well-trained in discipline, and to be well-spoken This is the highest blessing.
A little bit on a thread of Jesse’s carving lineage
Kamma in the Pali English Dictionary
kammasippi – artisan
kammarama – delighting in activity/work
History of the Buddha’s Begging Bowl
Part 2 of Buddha’s Begging Bowl
Northeast Indigenous Crooked Knife – Mocotaugan
Bill Reid’s Raven and the First Men
Blind Wood-Turner in Washington
Social Media
Here are some Instagram accounts of accomplished spoon-makers and such… more coming…
https://www.instagram.com/amy_umbel
Where our wood blanks came from:
https://www.instagram.com/emmet_van_driesche
This guy makes beautiful had-carved bowls…
More tools…
https://www.jasonalonontoolmaker.com